PLASTIC MACHINERY
PLASTIC EXTRUSION LINES
Plastic Extrusion produces items such as pipe/tubing, weather stripping, fencing, deck railings, window frames, plastic films and sheeting, thermoplastic coatings, and wire insulation. This process starts by feeding plastic material (pellets, granules, flakes or powders) from a hopper into the barrel of the extruder.
The material is gradually melted by the mechanical energy generated by turning screws and by heaters arranged along the barrel. The molten polymer is then forced into a die, which shapes the polymer into a shape that hardens during cooling process.
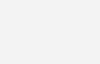

BLOWN FILM EXTRUSION
The manufacture of plastic film for products such as shopping bags and continuous sheeting is achieved using a blown film line. This process is the same as a regular extrusion process up until the die. There are three main types of dies used in this process:
- Annular (crosshead): Annular dies are the simplest, and rely on the polymer melt channeling around the entire cross section of the die before exiting the die; this can result in uneven flow.
- Spider: Spider dies consist of a central mandrel attached to the outer die ring via a number of “legs”; while flow is more symmetrical than in annular dies, a number of weld lines are produced which weaken the film.
- Spiral: Spiral dies remove the issue of weld lines and asymmetrical flow, but are by far the most complex.
SHEET OR FILM EXTRUSION
Sheet or film extrusion is used to extrude plastic sheets or films that are too thick to be blown. There are two types of dies used: T-shaped and coat hanger. The purpose of these dies is to reorient and guide the flow of polymer melt from a single round output from the extruder to a thin, flat planar flow. In both die types ensure constant, uniform flow across the entire cross sectional area of the die. Cooling is typically by pulling through a set of cooling rolls (calendar or “chill” rolls). In sheet extrusion, these rolls not only deliver the necessary cooling but also determine sheet thickness and surface texture.
Often co-extrusion is used to apply one or more layers on top of a base material to obtain specific properties such as UV-absorption, texture, oxygen permeation resistance, or energy reflection.


TUBING EXTRUESION
Extruded tubing, such as PVC pipes, is manufactured using very similar dies as used in blown film extrusion. Positive pressure can be applied to the internal cavities through the pin, or negative pressure can be applied to the outside diameter using a vacuum size to ensure correct final dimensions.
Additional lumens or holes may be introduced by adding the appropriate inner mandrels to the die.
OVER JACKETING EXTRUSION
Over jacketing extrusion allows for the application of an outer layer of plastic onto an existing wire or cable. This is the typical process for insulating wires. There are two different types of die tooling used for coating over a wire, tubing (or jacketing) and pressure. In jacketing tooling, the polymer melt does not touch the inner wire until immediately before the die lips. In pressure tooling, the melt contacts the inner wire long before it reaches the die lips; this is done at a high pressure to ensure good adhesion of the melt.
If intimate contact or adhesion is required between the new layer and existing wire, pressure tooling is used. If adhesion is not desired/necessary, jacketing tooling is used instead.

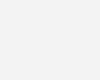
CO- EXTRUSION
Co-extrusion is the extrusion of multiple layers of material simultaneously. This type of extrusion utilizes two or more extruders to melt and deliver a steady volumetric throughput of different viscous plastics to a single extrusion head (die) which will extrude the materials in the desired form.
This technology is used on any of the processes described above (blown film, over jacketing, tubing and sheet). The layer thicknesses are controlled by the relative speeds and sizes of the individual extruders delivering the materials.
EXTRUSION COATING
Extrusion coating is using a blown or cast film process to coat an additional layer onto an existing roll stock of paper, foil or film. For example, this process can be used to improve the characteristics of paper by coating it with polyethylene to make it more resistant to water.
The extruded layer can also be used as an adhesive to bring two other materials together. Tetrapack is a commercial example of this process.
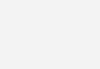